Maintenance Contracts
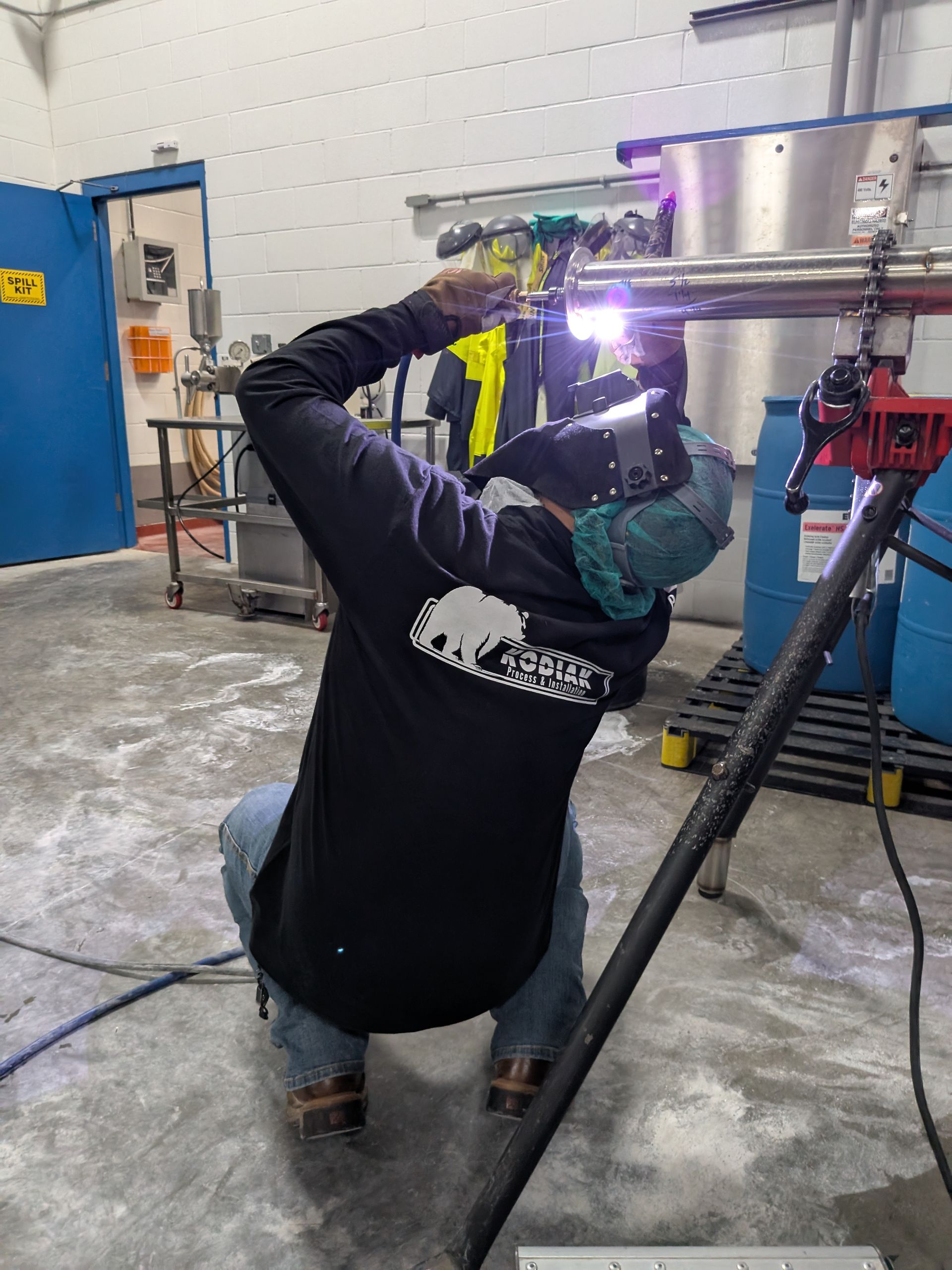
COMPREHENSIVE MAINTENANCE & SUPPORT SERVICES
- Scheduled Maintenance Visits – Dedicated technicians regularly service your plant.
- On-Call Support – Ready to respond anytime an issue arises.
- Preventative Maintenance – Identifying and fixing potential problems before they cause downtime.
- Expert Welding & Repairs – Skilled professionals handling sanitary and structural welding needs.
- Emergency Response – Quick mobilization to minimize disruptions.
- Equipment & Piping Inspections – Ensuring system integrity and compliance.
- Customized Service Plans – Tailored contracts to fit your plant’s specific needs.
- Minimized Downtime & Increased Efficiency – Keeping your operations running smoothly.
- Experienced & Reliable Team – Dependable professionals familiar with your facility.
Preventative Maintenance Insights
Easily
Accessible
Status Updates
Reduced
Unexpected
Downtime
Efficient
Maintenance
Scheduling
Value of Preventive Maintenance in Processing Plants
Preventive maintenance is crucial in processing facilities to ensure equipment reliability, maintain product quality, and comply with stringent food safety regulations. Regular maintenance helps prevent unexpected equipment failures, reduces downtime, and ensures consistent production schedules.
Industry Insights
- Maintenance Strategies: Dairy processing plants often implement a combination of preventive and predictive maintenance strategies. Preventive maintenance involves scheduled servicing of equipment, while predictive maintenance uses data analytics to predict equipment failures before they occur.
- Regulatory Compliance: Adhering to preventive maintenance schedules is essential for compliance with food safety standards such as those set by the FDA and USDA. Regular maintenance ensures that equipment operates within the required sanitary conditions.
- Operational Efficiency: Implementing effective preventive maintenance programs can lead to improved operational efficiency. By reducing unexpected breakdowns, plants can maintain steady production flows and meet market demands more reliably.
Common Preventive Maintenance Practices
- Routine Inspections: Regular checks of equipment to identify wear and tear.
- Scheduled Servicing: Timely replacement of parts and lubrication of machinery.
- Cleaning Protocols: Ensuring all equipment is cleaned according to established sanitary standards to prevent contamination.
- Record Keeping: Maintaining detailed logs of maintenance activities for accountability and regulatory purposes.